ALL SYSTEMS GO!
KERI ALLAN UNCOVERS HOW A NEW DIGITAL THREAD SORTING SOLUTION IS HELPING POSTNORD USE ITS DATA TO OPTIMIZE ITS AUTOMATED SORTING PROCESSES
Improving operational efficiency in a sorting center is always front of mind for managers, but it can often be challenging. At PostNord’s Hakkila terminal in Finland, for example, management faced challenges when trying to optimize the facility’s sorting processes.
The terminal had problems maintaining operational quality, due to site design, fluctuating volumes and changing management and processes. There was also a lack of oversight of resource use and process compliance, and an inability to measure performance.
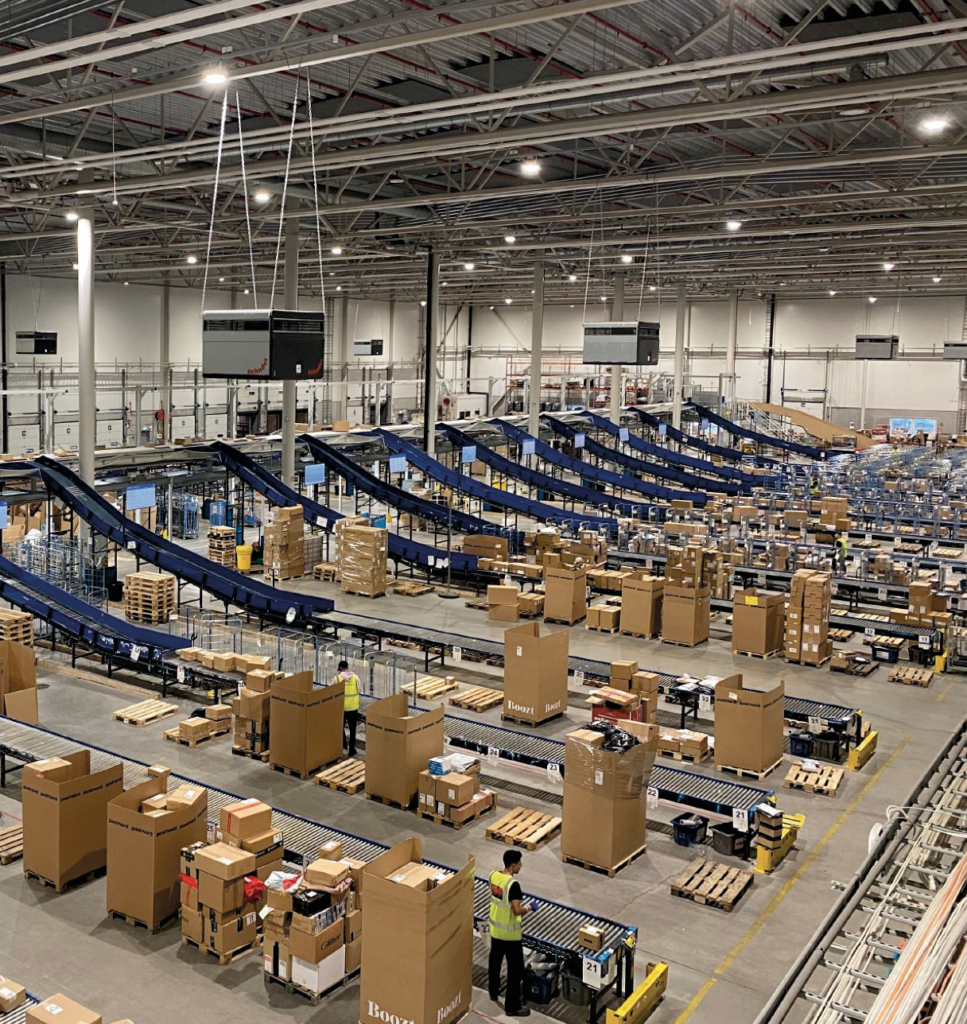
“The terminal was fairly new but had become congested quickly due to the volumes coming in,” explains Christian Østergaard, PostNord’s lead visionary and senior group strategist. “They had just gone through their first peak, which management felt had been quite disorganized and inefficient, so they reached out to our team to see how we might help them address issues around productivity, throughput and efficiency.”
The timing couldn’t have been better for Østergaard and his colleagues as they had something new they wanted to trial: a digital thread sorting solution.
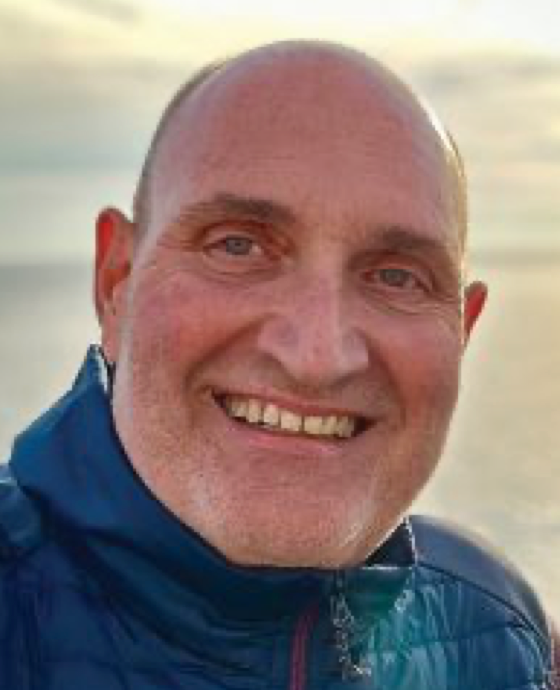
”WE WANTED TO BE ABLE TO MONITOR ALL OUR INTERNAL PROCESSES AND TO SEE WHERE OUR WORKERS WERE, TO SEE IF THE PROCESSES WERE OPTIMAL”
Christian Østergaard, PostNord
When looking to improve operational efficiency, the focus is often on working out which of the many sorter and process flow configurations is optimal for a specific facility. However, what is regularly overlooked is improving visibility across the site – of everything from execution flows and resource allocation through to movements and internal transportation.
Most managers won’t have access to such information, which means decisions are often based on personal experience or a ‘gut feeling’, and will differ from leader to leader. Being in constant operational mode also limits managers’ ability to think about these details, which is why PostNord wanted to trial this new solution, which would introduce more data-driven ways of working and just-in-time thinking.
Digital thread sorting solution
PostNord’s digital thread sorting solution creates a real-time representation of the entire sorting center across all assets and moving parts, thereby improving the understanding of process flows.
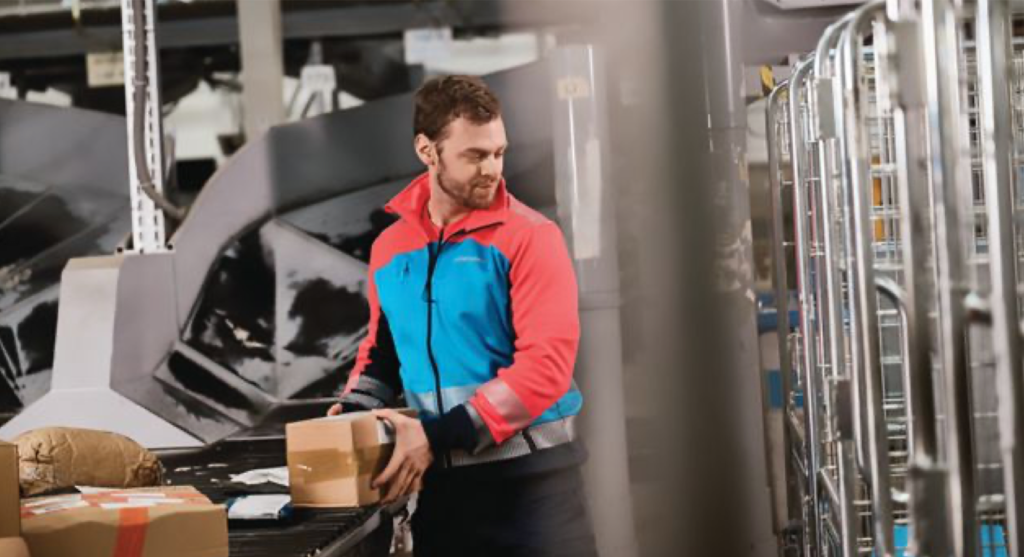
LEFT: The digital thread sorting solution uses a real-time location system to ensure workers are in the optimal place.
RIGHT: The solution enables PostNord staff to quickly identify areas of concern within the sorting machines
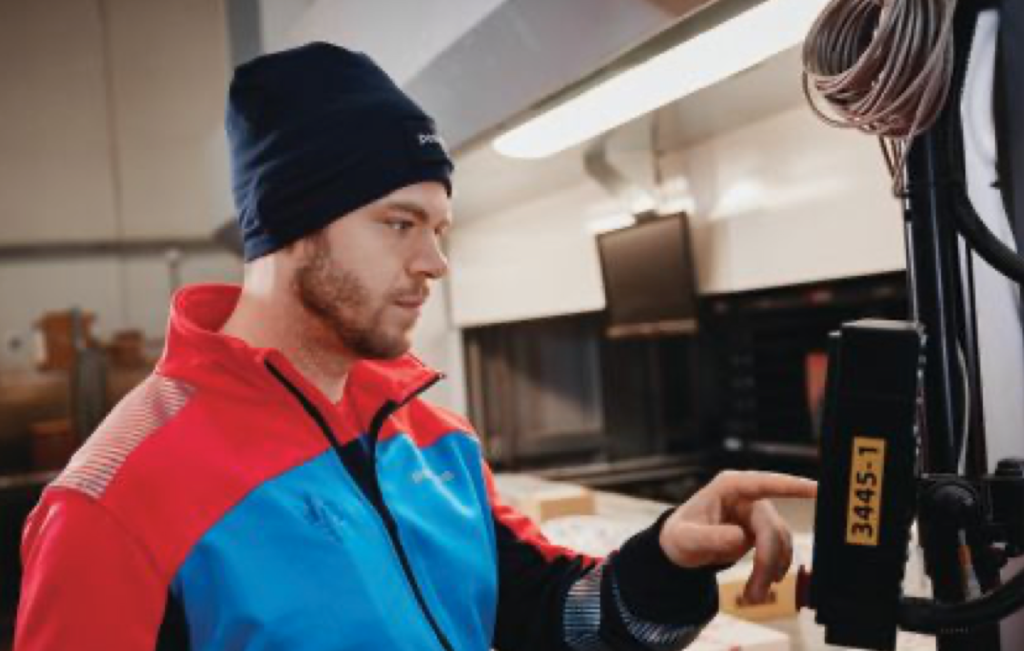
It is the result of several technology projects across the organization that Østergaard and his colleagues realized could be amalgamated and developed into an overarching sorting solution.
“The idea was to use computer vision together with a real-time location system (RTLS),” Østergaard explains. “Putting sensors in different places across the terminal would enable us to collect data in real time. We wanted to be able to monitor all our internal processes and to see where our workers were, to see if the processes were optimal or whether there was room for improvement.”
Digital thread benefits
- An operational efficiency gain of more than 25% in sorting operations
- A 32% increase in the number of parcels sorted per hour
- Percentage of sorting staff meeting KPIs has risen from 20% to 54%
- ROI of technology pilot was less than four months
Gaining trust
The rollout of the digital thread sorting solution took place in stages, working in close collaboration with the local management team.
“When you come in with a new technology, it’s important to gain the trust of the people who will use it. We had a list of the things we wanted to do but began by asking them if they had specific problems that they wanted us to look at,” Østergaard reports.
“They raised two areas of concern: an underperforming machine and making sure the first-in, first-out principle was being used when it came to storage. For the first issue, we were quickly able to establish functions that enabled staff to see what was going wrong in the process, so it could be resolved. For the second, we visualized things for them, so they could see what was happening. This built the trust and it then became a question of okay, how do we go ahead and roll out everything else?”
At each stage of the rollout, solutions were reviewed and tweaked if necessary. “It was a great collaboration, where there was the strategic team looking at how we can get the technology to work, our partner vendors, who were focused on making it work, and the local tech-savvy management, who were keen to use technology to improve efficiencies,” comments Ravi Kiran Kotty, digital transformation technology strategist at PostNord.
“They’d say, ‘Okay, we think we can be more efficient here’, and we’d sit down and come up with a solution. If the first iteration didn’t work exactly as they wanted, then we reconfigured it so that it was fit for their purpose.
“It was a slow evolution,” Kotty continues. “We went use case by use case. Once it was implemented, we would evaluate whether it added value before moving on to the next one. We’d identify an asset, try to generate data from it, then the value, before looking to add additional assets. There was no big bang, it was a progressive thing, which added value exponentially with every use case.”
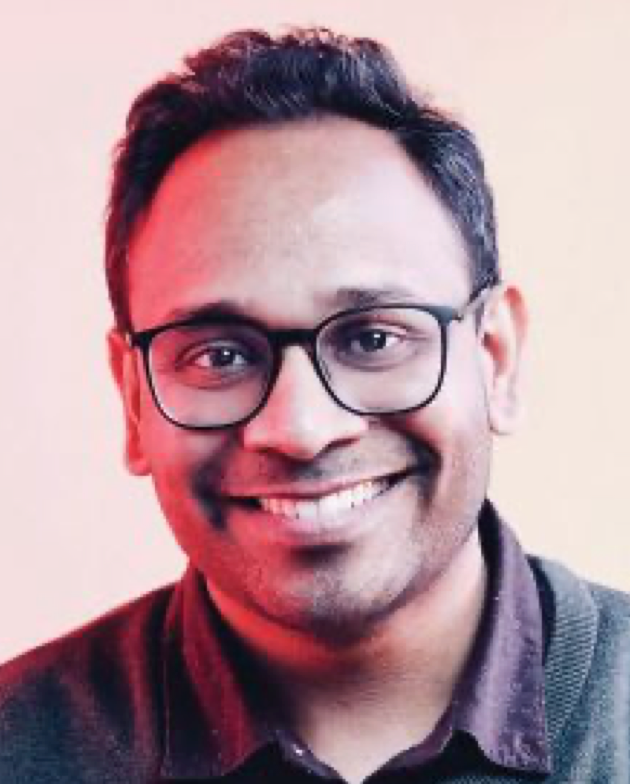
”EVERYONE LIKES SIMPLICITY. THEY DON’T WANT A LOT OF DATA, JUST QUICK ANSWERS OR SIMPLIFIED GUIDANCE”
Ravi Kiran Kotty, PostNord
A collaborative partnership
After launching its new sorting facility in September 2022, PostNord faced challenges with productivity KPIs such as parcel throughput and production efficiency. The need for reliable tracking and monitoring led to the implementation of Quuppa’s RTLS technology. By tracking mobile devices and forklifts, PostNord gained real-time visibility of transportation movements and resource allocation, especially in critical areas like sorting machines and cross-docking zones. This visibility allowed for the identification of process inefficiencies, enabling optimization of workflows.
The collected KPIs and analytics are computed in near real time and provided directly to the relevant people within the facility, allowing PostNord to optimize work floor and sorting chute handling, monitor the number of trips between overflow chutes and improve the use of the cross-docking areas. These improvements have resulted in a more than 20% increase in efficiency and productivity.
The technology also enables data-driven decision-making, moving away from guesswork to fact-based planning. Real-time insights allowed better resource allocation and shift planning, improving operational processes and reducing internal lead times. This shift has helped PostNord to achieve higher delivery quality and improve parcel throughput.
By integrating the system into a digital twin model, PostNord has advanced toward its 2032 vision of touchless parcel handling, improving both operational efficiency and sustainability.
PostNord partnered with two key vendors on the development of the digital thread solution: Tata Consultancy Services (TCS) and Quuppa. TCS helped the post build its computer vision models, while Finnish startup Quuppa provided high-precision indoor tracking technology (see Real-time asset tracking below).
Work on the project began back in May 2023, with the digital thread solution completed by the end of January 2024. The biggest integration of new technology into the terminal was the installation of Quuppa’s RTLS technology. This entailed a full site survey to assess what was needed in terms of physical infrastructure.
“The first part was installation, which took some time, but after that we were able to deliver new use cases every couple of weeks,” Kotty notes.
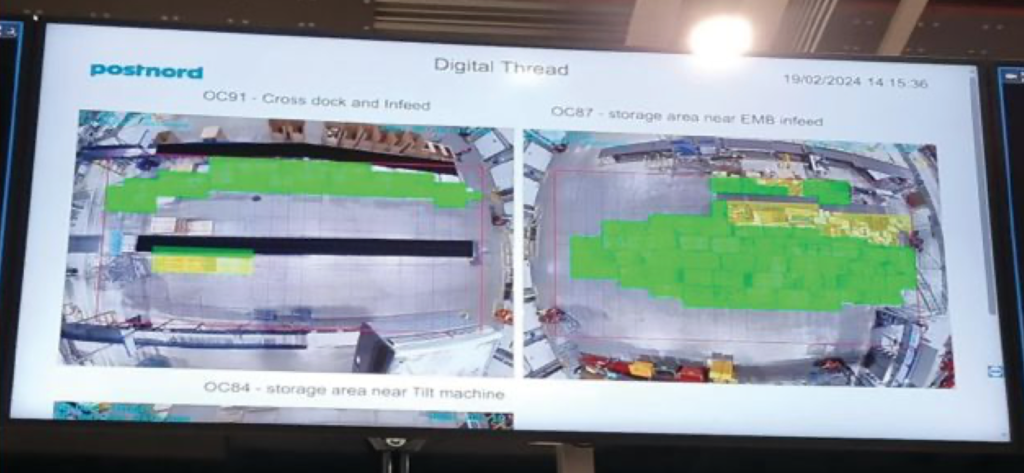
ABOVE: The solution provides a real-time overview of parcel volumes.
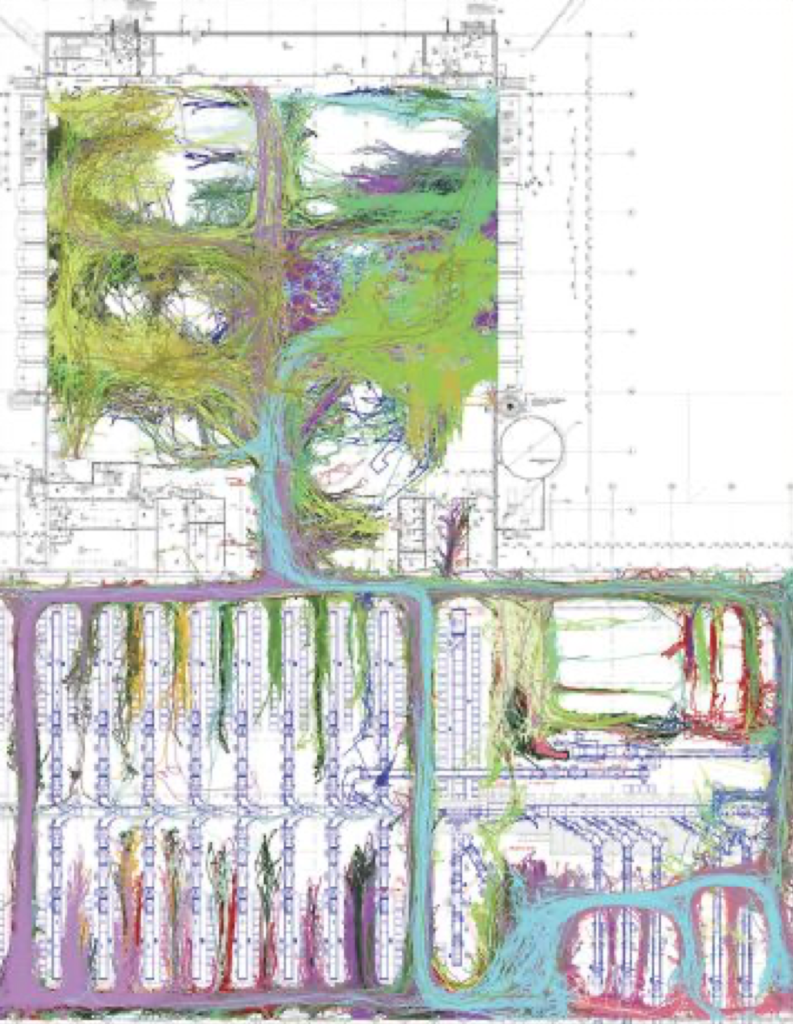
LEFT: A spaghetti diagram of internal transportation volume in the sorting terminal.
One of the first use cases was employing PostNord’s existing security camera system to monitor movements and processes, to identify areas of concern. “The good thing with computer vision is that if you already have the cameras, you just need to introduce an ‘intelligent filter’ that is trained in what to identify and measure,” says Østergaard.
Improving visibility
PostNord says the digital thread is helping to measure two key areas: productivity and internal transportation. Productivity is assessed in an anonymized way, examining processes and supporting functions using existing handheld devices.
“We don’t want to know who each worker is – we simply want to know where people are and what they are doing at any given time. We ‘Smurf’ them, because our system shows them as blue,” Østergaard chuckles.
This enables management to see whether the site or workflow is designed in a way that adds leakage. They can also evaluate different processes and identify any wasted productivity and the reason behind it.
In terms of internal transportation, visualization, control points, flow optimization and new data help PostNord achieve better use of assets like forklifts, employees and floor space.
Benefits to all
The digital thread benefits all levels of staff, from those on the shop floor through to shift leaders and process designers. The business case has already been proved at Hakkila, where the terminal has seen a more than 25% increase in operational efficiency in sorting, in addition to increased productivity, improved quality, the removal of bottlenecks and the establishment of performance measurement.
“We regularly check in with the Hakkila team and each time we speak they’ve consistently improved,” enthuses Kotty.
“That’s possible because we’ve created a ‘blue ocean’ of data; some that had never been looked at before,” Østergaard adds.
A standout use case at Hakkila has been the introduction of a simple traffic light system to communicate needs to terminal staff. PostNord has a staff turnover of 8% a month in this specific terminal, so it needed something straightforward and self-explanatory that everyone could understand straight away. It therefore introduced a visual tool where screens show areas of the facility as green (low attention), yellow (high attention) or red (critical) to let staff easily see where they’re needed. “If they see a red or yellow area on the screen, they know they can be useful there. This visualization enables them to make better use of themselves without the need for management to intervene,” continues Østergaard.
By giving staff continuous information on where they were most needed, the number of parcels they could handle per hour increased by almost 30%, notes Kotty. In addition, before the introduction of the traffic light tool, only 20% of those on the floor were able to meet the KPI targets PostNord had set – now 54% can. “They’re able to work more efficiently,” he enthuses.
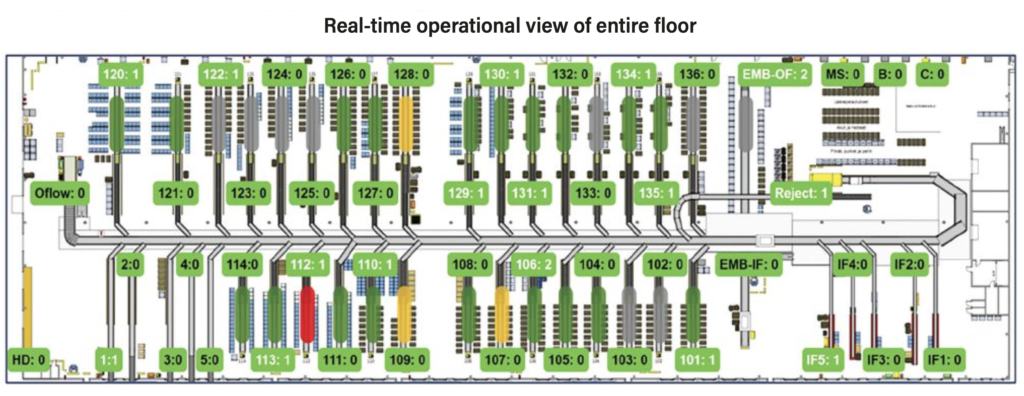
ABOVE: A traffic light visual tool ensures the system is easy for new staff to understand
Modern image
The introduction of the digital thread has had a positive impact on the company’s image, with many employees saying that they regard PostNord as a modern employer.
“Many of our employees are gamers; they have a vacuum cleaner robot at home; they’re tech savvy and have an expectation that their employer will be too.
So it’s been very positive for the company’s brand,” explains Østergaard. “It’s also easier to teach people new functions.”
“Indeed, we always want to trust simplicity rules, and this project helped us validate that,” notes Kotty. “Everyone likes simplicity. They don’t want a lot of data, just quick answers or simplified guidance.
“The ROI is between three and four months, again validating this as a good approach to take. Of course, there are a couple of prerequisites: you need an organization that’s tech savvy, and people who are open to change and will support your implementation. But there are not many use cases where you can see productivity increases of this ratio, with this kind of payback.”
What lessons has POSTNORD learned?
- Tech-savvy local management and workers are key to implementing and adopting new technology in operations
- You can make use of lots of your existing infrastructure to gain new insights into how your processes are running
- Collaboration between all parties is essential
- Keep communication of data simple and straightforward
Next steps
The development of the digital thread is an important step toward hyper-automation of PostNord’s terminal operating execution model. The post says it’s been a perfect playing field for operations, innovation and IT to evaluate and implement the right changes and at the right time.
It plans to continue bringing many of its use cases together as part of the digital thread, including asset tracking, forecasting and digital twins.
Based on the success at Hakkila, PostNord is now rolling out the digital thread solution in Denmark. Once the first site has been successfully completed, the plan is to scale it to the country’s two largest terminals.
This Case Study was originally published on Parceland Postal Technology International March 2025 p. 44.