BACKGROUND
Founded in 1979, KISSEL Spedition GmbH constructed a new logistics site in Mainaschaff, Germany, in 2021. The family-owned company now has modern logistics facilities, including a new 9,000 m2 transhipment hall with 82 hall doors as well as a new 5,000 m2 logistics warehouse with 5,500 pallet slots and 42 vehicles or forklifts. About 350 professionals deliver logistics services at the site and process 7,000 packages daily.
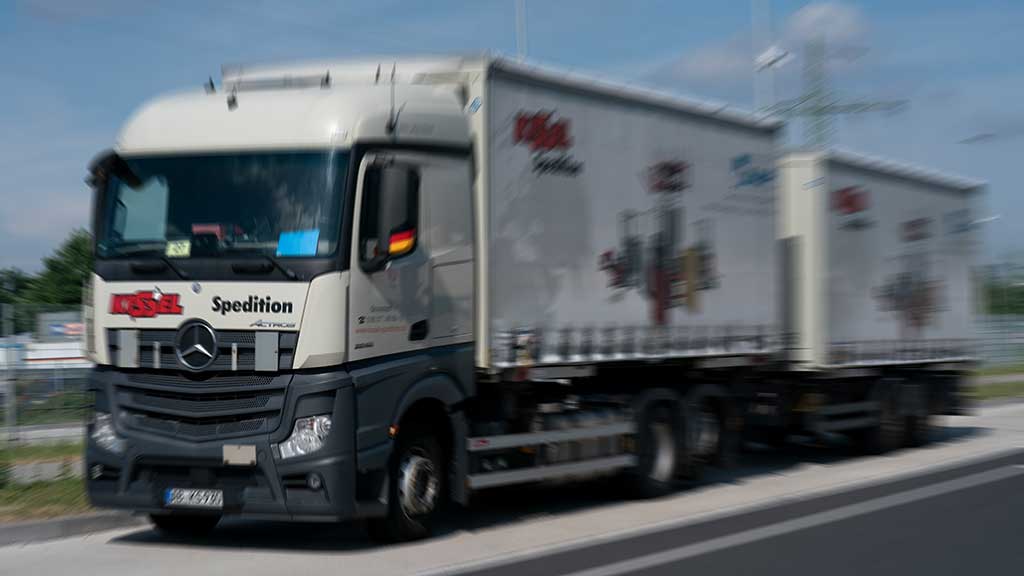
CHALLENGE
KISSEL Spedition wanted to improve the operational performance, process automation and safety in their services and operations. Efficient logistics requires functional facilities and modern information technology solutions. KISSEL Spedition offers a wide range of logistics services and has invested heavily in modernising their logistics infrastructure and processes.
KISSEL Spedition wanted to improve the operational performance, process automation and safety in their services and operations. Efficient logistics requires functional facilities and modern information technology solutions. KISSEL Spedition offers a wide range of logistics services and has invested heavily in modernising their logistics infrastructure and processes.
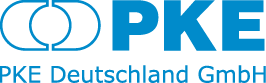
The company works closely with PKE Deutschland GmbH, their information technology partner. In today’s digitalised logistics business, assets can and need to be tracked in all areas within the buildings. The logistics company wanted to make relevant information available more quickly and easily to all professionals and drivers working in Mainaschaff, whenever and wherever it is needed. The goal was to utilise indoor location technologies and automation as smart as possible with the help of PKE’s professionals.
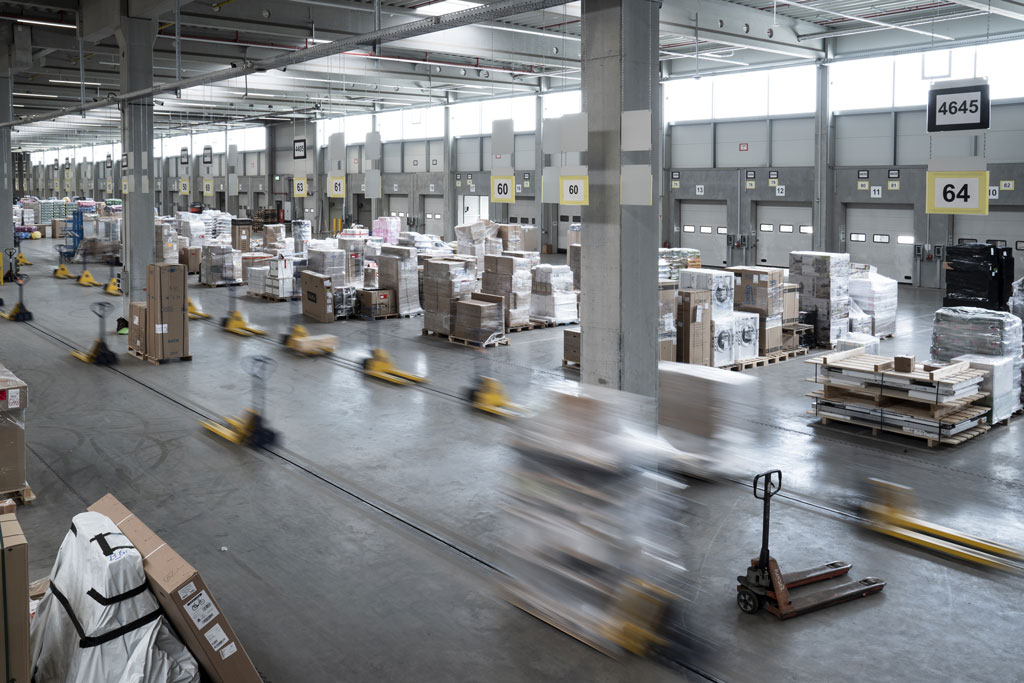
SOLUTION
With the help of PKE, KISSEL Spedition was one of the first pioneers in logistics to implement a FullHD IP-based camera system in its operations in 2009. Today, KISSEL Spedition uses advanced software and hardware, including 207 IP cameras both inside and outside the buildings. PKE supplied Mainaschaff the Video, Locating and Software (VLS) system, including the indoor locating system powered by Quuppa. The robust and reliable system tracks scanners, forklifts and pallets 24/7.
The Bluetooth function is installed into the scanners by default and, in combination with the VLS system, provides real-time location information directly into the application. When pallets arrive in the weighing area, the VLS system automatically sends the information into the weighing application. The stored location data can be combined with the data received from the video cameras. The indoor cameras deliver images from all scanners into the transhipment application SLS providing employees direct access to the data.
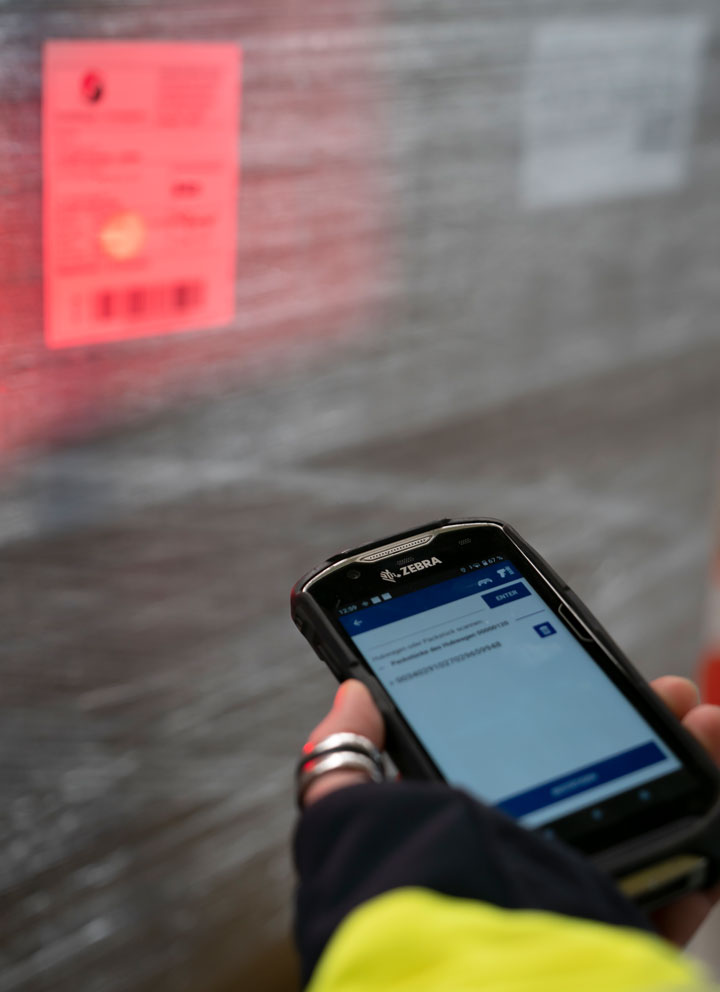
The inventory of all pallets can be done fully automated every day. All vehicles and forklifts can be identified when they arrive, for example, at a hall gate enabling automated access control. The warehouse office area and 50 hall doors have been equipped with access control and automatic alerts in case of breaches.
RESULTS
The PKE solutions powered by the Quuppa indoor tracking system fulfil many business requirements at KISSEL Spedition’s challenging logistics indoor environments.
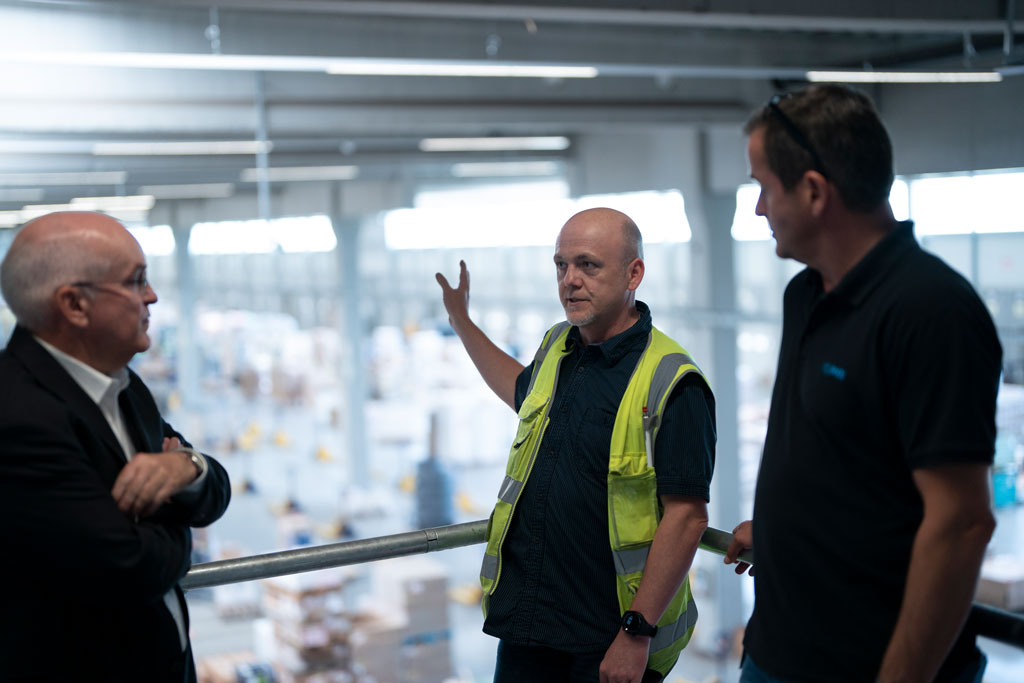
The accurate, continuous and dynamic tracking solutions offer several benefits to KISSEL Spedition:
- Gives a new dimension to a fast-paced logistics environment by reporting the positions of scanners, pallets and vehicles in real time.
- Improves the operational logistics performance and the automation level at the site.
- Allows logistics professionals to get the needed information faster.
- Enhances cooperation and saves time.
- Automates processes and improves site security.
NEXT STEPS
As a next development step, KISSEL Spedition plans to implement the AVASYS® security management system introduced by PKE. The system centrally steers the security technologies and connects them with other systems like the weighing application and the building automation and services systems.
For more information, visit v-l-s.com