In today’s rapid and sometimes chaotic industrial environments, tracking assets in real time is essential to optimize operations, maximize efficiency and reduce cost. Real-time location systems (RTLS) have proved valuable for these purposes, but recent advancements offer new potential for the technology.
Think of RTLS as the GPS of the industrial world, providing insights into the movement and location of equipment and assets, tracking everything from forklifts to shipping containers to consumer goods, indoors and outdoors. But instead of solely capturing asset coordinates, modern RTLS systems offer displays to communicate asset information in real time, showing where an asset has been and where it needs to go.
I’d like to explain more about data visualization with RTLS—and what problems can be overcome using it—with what I imagine is the next biggest trend in industrial logistics.
How To Visualize Data
While the visualization of location data in logistics is still in its early stages, digital displays tied to real-time information are already the norm in other vertical markets. Consider the recent adoption of electronic shelf labels (ESLs) in retail spaces, particularly at grocery stores. Food products are marked with digital labels to accurately reflect the unit price, daily discounts and stock availability, along with other relevant product information.
With the advent of ESLs, we’ve seen a major shift away from paper toward digital price tags; generally, these displays are more sustainable and less resource-intensive to maintain and operate.
But what’s the relevance of these displays to manufacturing? Mostly, data visualization tools enhance industrial RTLS projects by providing instructions in an easily accessible format and improving process flow.
Such instruction can be achieved by attaching digital displays to transport units—whether it’s a box, roller cage or palette—to reveal dynamic real-time information on asset storage and movement. For example, if an employee takes a forklift of boxes to the wrong location in a warehouse or on a factory floor, the display on the forklift, or the display directly mounted on the boxes, will change the text in real time to say “wrong destination, take me to this location instead.”
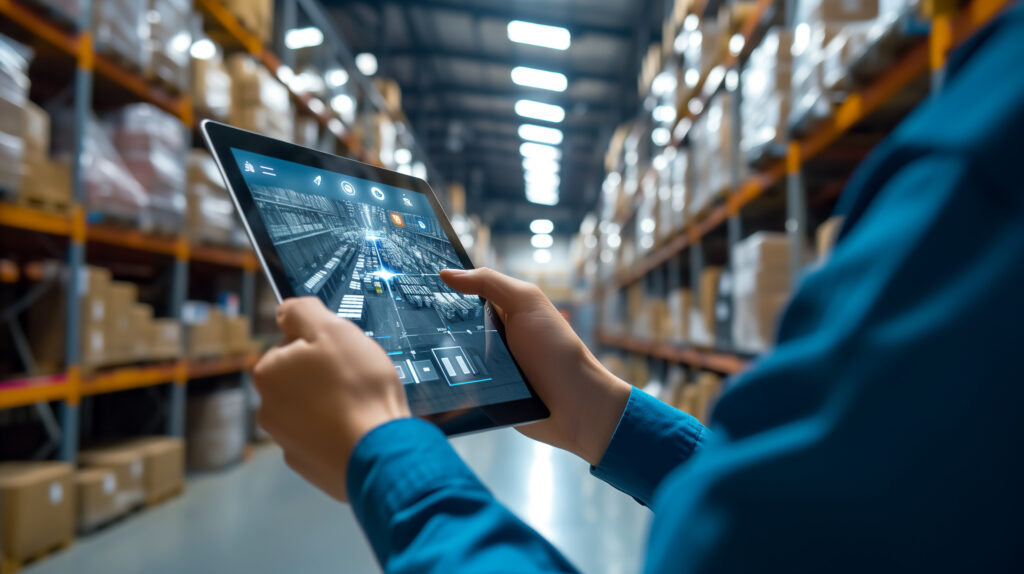
A more simplified example of this is pick-to-light technology: If an employee comes close to something they should grab, the display blinks at them. Digital location displays don’t necessarily have to display text, they can also be scannable barcodes or QR-codes that are displayed and dynamically updated or have a blinking LED light.
Why Visualize Data
With this advanced RTLS system in place, employees on the operations floor receive immediate dynamic feedback on whether they’re executing the right process or completing the right task. This all brings direct benefits to process optimization, reducing search time and minimizing human errors. Overall, a display tag guides an employee’s immediate actions to improve process flow across a facility.
Digital displays can also be leveraged to improve inventory management. By using electronic tags and displays, manufacturing plants and warehouses can track goods at every stage of the production process, both on the backend postal applications, as well as directly from the facility floor. Digital displays provide real-time information on inventory levels, locations and movements, ensuring resources are used efficiently and reducing the need for overstocking and waste.
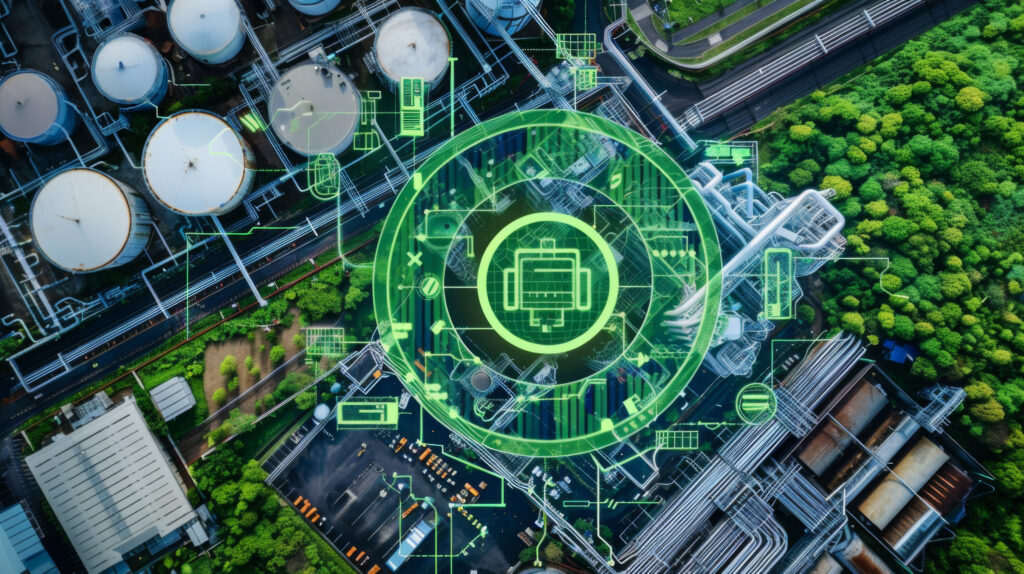
Data visualization may also play a crucial role in improving sustainability along the supply chain. By tracking the movement of goods in real time, logistics providers can identify opportunities to reduce waste and optimize resource usage. Moreover, digital displays also reduce paper waste and related inefficiencies. Instead of constantly changing paper tags as asset information changes, the tag remains the same but the information displayed on it transforms.
Challenges To Implementation
While RTLS coupled with digital displays offers significant benefits, their implementation isn’t without challenges. Understanding and addressing these concerns is essential for a successful deployment.
For one, implementing RTLS requires substantial investment in both technology and facility modernization. Many companies aspire to achieve digitization, Industry 4.0 standards, sustainability and reduced CO2 footprints. However, realizing these benefits necessitates upgrading infrastructure, which can be costly and time-consuming. Organizations need to carefully assess their readiness for such investments and plan for gradual integration to manage costs effectively.
Facilities also need to be prepared to analyze and leverage large amounts of data. RTLS generates vast amounts of data and insights into process flows, which can be overwhelming if not managed properly.
The key to leveraging this data is integrating it into existing processes and adapting performance metrics and reporting mechanisms accordingly. Organizations must establish robust data analysis frameworks and be prepared to act on the insights provided by RTLS. This requires a top-down mandate to drive change across the organization.
However, such mandates may not be well received. Introducing RTLS and digital displays in an industrial environment may meet resistance from employees who are accustomed to existing processes. Workers may feel that their knowledge and expertise are being undervalued. This mindset can create friction when new technologies are introduced.
However, it’s crucial to communicate that RTLS is not about replacing the workforce but enhancing their efficiency and streamlining their workflow.
Moving Forward
The integration of digital displays with RTLS is part of a wider global trend shifting away from static paper labels with outdated information to smart displays with dynamic information.
In logistics, that means asset information—be it product specs, expiration or shipping information—is clearly displayed with an asset anywhere in the facility. The goal is to optimize the process while minimizing unnecessary costs and efficiencies
In essence, this advancement enables the right information to be in the right place at the right time. That’s what RTLS is all about.
This article was originally published on Forbes.com.